Toyota RAV4 (XA40) 2013-2018 Service Manual: Differential case
Components
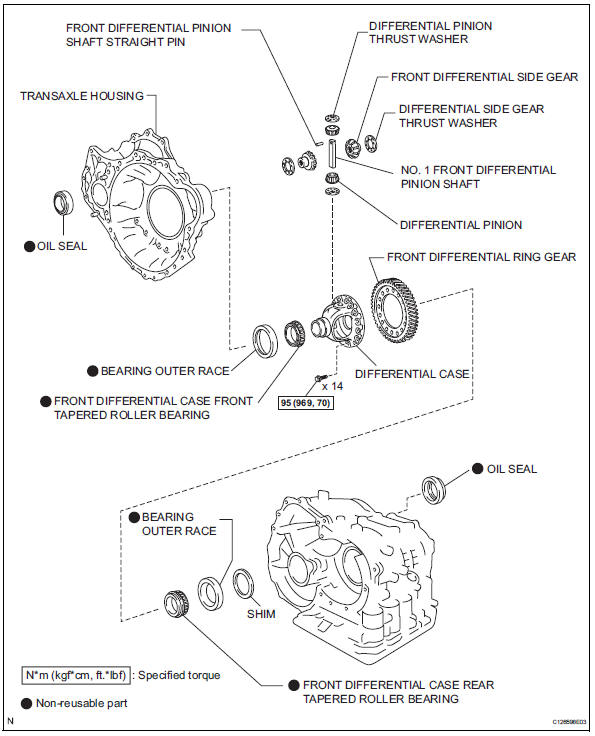
Disassembly
- Remove front differential ring gear
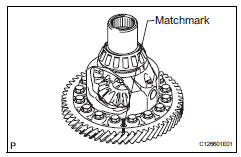
- Place the matchmarks on the ring gear and
differential case.
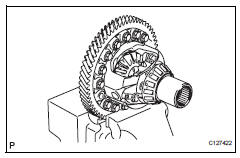
- Remove the 14 bolts.
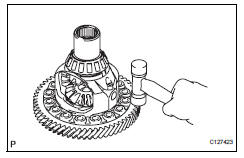
- Using a plastic-faced hammer, tap on the ring gear
to remove it from the case.
- Remove front differential case front tapered
roller bearing
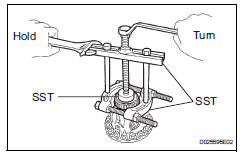
- Using sst, tap out the front differential case front
tapered roller bearing from the differential case.
Sst 09950-00020, 09950-00030, 09950-60010
(09951-00500)
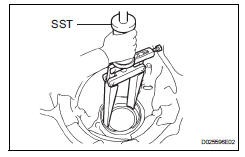
- Using sst, remove the front differential case front
tapered roller bearing outer race.
Sst 09308-00010
- Remove front differential case rear tapered
roller bearing
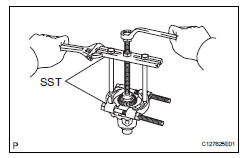
- Using sst, remove the front differential case rear
tapered roller bearing from the differential case.
Sst 09950-00020, 09950-00030, 09950-60010
(09951-00500)
- Using sst, tap out the front differential case front
tapered roller bearing outer race.
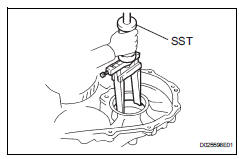
Sst 09308-00010
- Remove front differential pinion shaft
straight pin
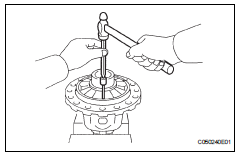
- Using a pin punch and hammer, tap in the straight
pin.
Notice:
Before removing the straight pin, unstake it with
a pin punch.
- Remove no. 1 Front differential pinion shaft

- Remove the front differential pinion shaft from the
differential case.
- Remove front differential side gear
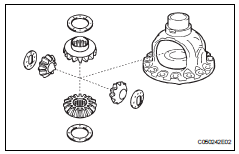
- Remove the 2 front differential pinions, 2 pinion
thrust washers, 2 front differential side gears and 2
side gear thrust washers from the differential case.
- Remove transaxle housing oil seal
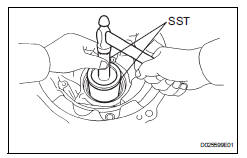
- Using sst and hammer, tap out the oil seal.
Sst 09950-70010 (09951-07100), 09215-00013
(09215-00471)
- Remove differential side bearing retainer oil seal
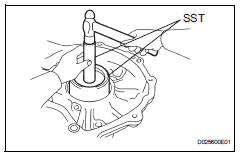
- Using sst and hammer, tap out the oil seal.
Sst 09950-70010 (09951-07100), 09608-10010
Inspection
- Inspect differential side gear backlash
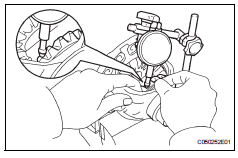
- Using a dial indicator, measure the backlash of the
side gear.
Standard backlash:
0.05 To 0.20 Mm (0.0020 To 0.0070 In.)
Standard thrust washer thickness

Reassembly
- Install front differential side gear
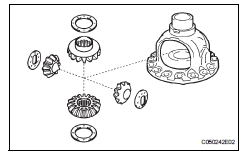
- Coat the 2 front differential side gears, 2 side gear
thrust washers, 2 font differential pinions and 2
pinion thrust washers with atf and install them to
the differential case.
- Install no. 1 Front differential pinion shaft
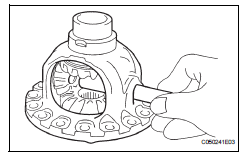
- Coat the no. 1 Front differential pinion shaft with
atf, and install it to the differential case.
- Install transaxle case straight pin
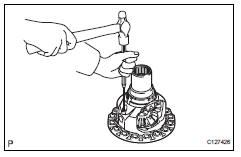
- Using a pin punch and a hammer, tap in the pinion
shaft straight pin.
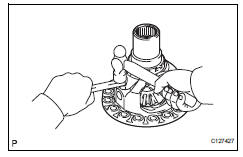
- Using a chisel and a hammer, stake the differential
case.
Notice:
Stake it after adjusting the backlash.
- Install front differential case rear tapered
roller bearing
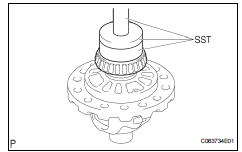
- Using sst and a press, press in the front differential
case rear tapered roller bearing to the differential
case.
Sst 09550-60010, 09950-60020 (09951-00680),
09950-70010 (09951-07100)
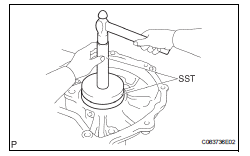
- Using sst and a hammer, tap in the front
differential case tapered roller bearing front outer
race to the transaxle housing.
Sst 09550-60010, 09950-60020 (09951-00680),
09950-70010 (09951-07100, 09951-00890)
- Install front differential case front tapered
roller bearing
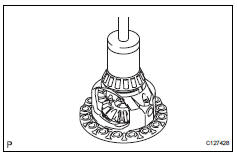
- Using sst and a press, press in the front differential
case rear tapered roller bearing to the differential
case.
Sst 09550-60010, 09950-60020 (09951-00680),
09950-70010 (09951-07100, 09951-00890)
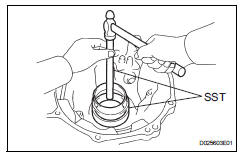
- Using sst and a hammer, tap in the front
differential case tapered roller bearing front outer
race to the transaxle housing.
Sst 09550-60010, 09950-60020 (09951-00680),
09950-70010 (09951-07100, 09951-00890)
Notice:
Clearance is not allowed between the bearing
and transaxle housing.
- Adjust differential side bearing preload
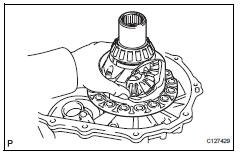
- Install the differential assembly to the transaxle
case.
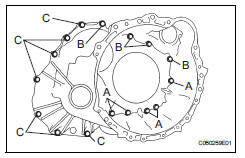
- Clean the matching surfaces of the transaxle case
and transaxle housing.
- Install the transaxle housing to the transaxle case
and tighten them with the 16 bolts
Torque: 22 n*m (224 kgf*cm, 16 ft.*Lbf) for bolt a
29 n*m (296 kgf*cm, 21 ft.*Lbf) for bolts
b and c
Hint:
Each bolt length is indicated below.
Bolt length:
50 Mm (1.969 In.) For bolt a
50 M (1.969 In.) For bolt b
42 Mm (1.654 In.) For bolt c
Notice:
Usually, bolt a is non-reusable bolt. In this case,
however, it can be used after cleaning it.
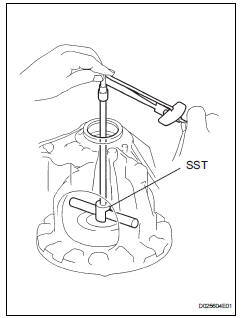
- Using sst, return the differential assembly right and
left 2 or 3 times to allow the bearing settle.
Sst 09564-32011
- Using sst and torque wrench, measure the turning
torque of the differential.
Sst 09564-32011
Torque: standard turning torque at 60 rpm
0.20 To 0.69 N*m (2.0 To 7.0 Kgf*cm, 1.8
To 6.1 In.*Lbf)
Hint:
If the turning torque is not within the specified value,
refer to the table below and select a thrust washer
which turning torque is within the specified value.
Standard flange thickness
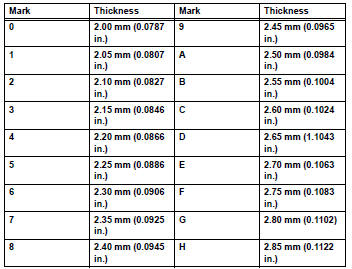
- Remove the 16 bolts and the transaxle housing.
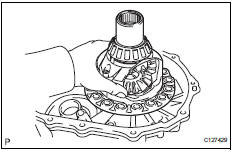
- Remove the differential assembly.
- Install front differential ring gear
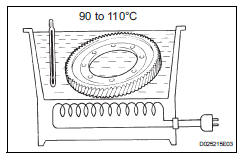
- Using atf and a heater, heat the front differential
ring gear to 90 to 110 °c (194.0 To 230.0 °F)
Notice:
Do not overheat the ring gear to 110°c (230.0°F)
or more.
- Clean the contract surface of the front differential
case.
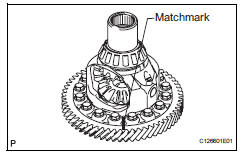
- Align the matchmarks, and install the front
differential ring gear case quickly.
Notice:
Do not install the bolts while the ring gear is hot.
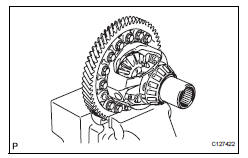
- Tighten the 14 bolts.
Torque: 95 n*m (969 kgf*cm, 70 ft.*Lbf)
Notice:
Tighten the bolts a little at a time in diagonal
order.
- Install differential side bearing retainer oil
seal
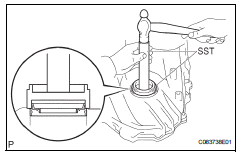
- Coat the lip of a new oil seal with a little amount of
mp grease.
- Using sst and a hammer, tap in the oil seal.
Sst 09223-15020, 09950-70010 (09951-07100)
- Remove transaxle housing oil seal
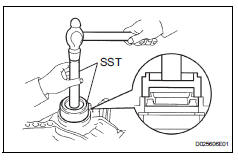
- Coat the lip of a new oil seal with a little amount of
mp grease.
- Using sst and a hammer, tap in the oil seal.
Sst 09710-30050, 09950-70010 (09951-07100)
Components
Disassembly
Remove shift solenoid valve slt
Remove the bolt, plate and shift solenoid valve slt
from the valve body.
Remove shift solenoid valve sl1
Rem ...
Other materials:
Voice command system
The voice command system enables the hands-free system to
be operated using voice commands.
Using the voice command system
Press the talk switch.
To cancel the voice command system,
press and hold the talk switch.
After a beep sounds, say the desired command.
On the list screen, ...
Short to b+ in can bus line
Description
There may be a short circuit between the can bus line and +b when there is
resistance between
terminals 6 (canh) and 16 (bat) or terminals 14 (canl) and 16 (bat) of the dlc3.
Wiring diagram
Inspection procedure
Notice:
Turn the ignition switch off before measuring ...
Luggage room light
Components
Removal
Disconnect cable from negative battery
terminal
Caution:
Wait at least 90 seconds after disconnecting the
cable from the negative (-) battery terminal to
prevent airbag and seat belt pretensioner activation.
Remove back door center garnish (see page
ed-59)
...